12月25日,在沈阳汇众汽车底盘系统有限公司生产科装配班组生产现场,班长李强在拧紧螺帽的同时,贴标机也同步完成了标签粘贴工作。“工作效率与之前相比大幅提升,每次操作减少了15秒,一天下来就能节省两个半小时,这在以前是无法想象的。”工段长张东月感慨地说。
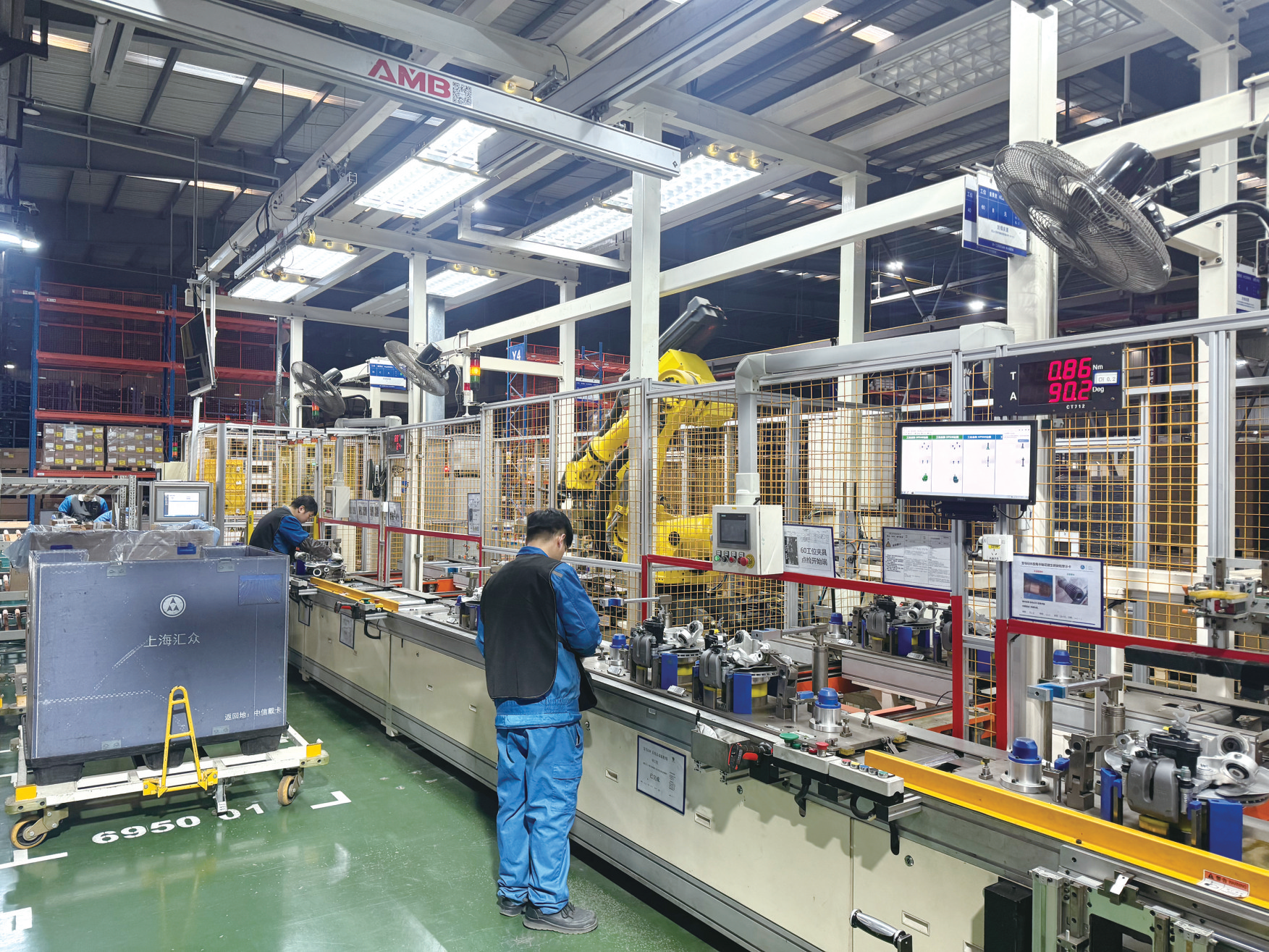
(图片来源:沈阳汇众汽车底盘系统有限公司)
曾经,该道工序的操作流程是:先由压机拧紧弹簧,然后人工操作电动扳手进一步拧紧螺帽,之后贴标机才能进行贴标。因3个环节相对独立,导致贴标机在人工拧紧螺帽的过程中有15秒的等待时间。
如何缩短或消除这一无谓的等待?2023年,李强带领装配班组成员反复研究,通过重新编程改变工序,实现了贴标机与人工拧紧螺帽同步进行。经过调整优化,整个生产流程更加高效,全年为公司节约成本38万元。
此外,装配班组还针对机器人拧紧螺栓后工件容易磕伤问题进行了改进。汽车底盘处一个重要零部件的4个螺栓是由机器人拧紧的。由于机器人和工装产生的巨大拉扯力,机器人手臂抬起时,往往会将工件一同带起,导致该零件在落下时容易磕伤,影响产品质量。面对这一问题,班组成员开展“头脑风暴”,终于找到了一个有效的解决方案:在零件与机器人中间增加一个反作用支撑杆。该支撑杆固定在机器人手臂上,避免工件被带起。改进后,产品合格率从97%提升到100%。
小改小革不断,创新成果涌现。装配班组还实施了27项防错项目,其中,扫描防错措施效果尤为突出。该项技术为每个产品的零件都设置了一个独一无二的二维码标签。在装配过程中,工作人员只需扫描二维码,系统便能迅速且准确地匹配出当前所需零件。一旦扫描到的零件与要求不符,系统会立即触发报警机制,有效杜绝“错配”情况的发生。
近年来,该班组在提升产品质量和效率方面贡献突出,获评沈阳工人先锋号荣誉称号。
来源:《辽宁工人报》(2024年12月27日 第04版)