沈阳航天三菱汽车发动机制造有限公司是由中国、日本、马来西亚三国五家公司出资组建的中外合资企业。生产技术准备部设备维修工段,成立至今已有21年之久,主要负责公司所有生产设备的故障维修和定期保养。在高效连续的生产任务中,生产设备24小时不停运转情况下,设备维修工段的成员们,凭借着扎实的技术能力、精益求精的工作态度和锐意进取的创新精神,出色的完成了各项维修任务,保证生产高效有序地进行,为公司发展做出了突出的贡献,得到了领导和其他部门同事的高度评价,并持续为公司安全高效的生产保驾护航。
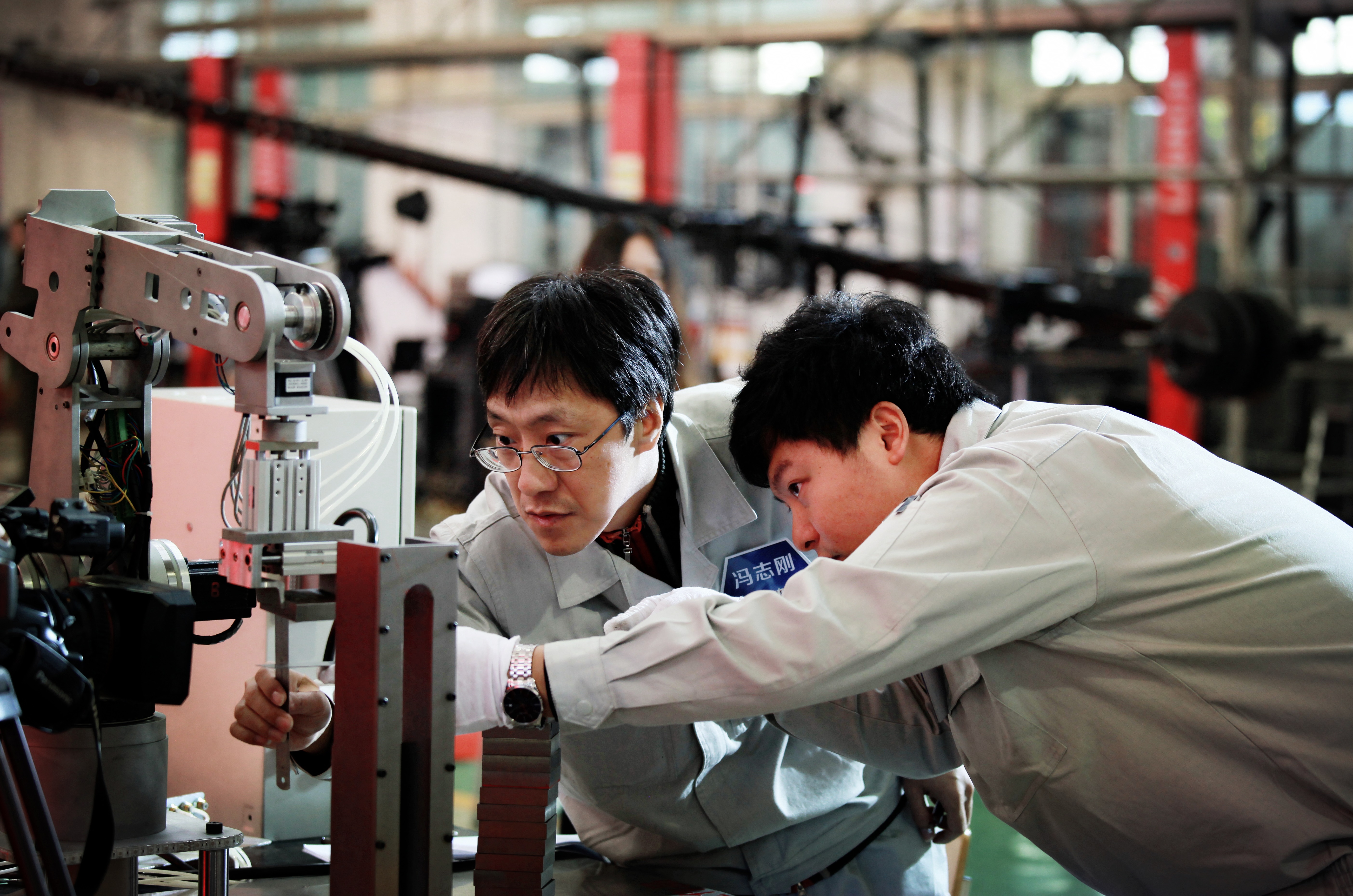
设备维修工段现有成员53人,分为3个抢修组、1个计划维修组和1个改善创新组,其中中共党员13名,高级技师12名,技师10名。
设备维修工段自成立起就开始承担公司所有生产设备的维修保养工作,包括毛坯铸造、精密机械加工、装配自动化生产线以及物流、开发、质管等各部门1100多台设备的维修和保养,其中国外进口自动化生产线设备达90%以上。为了保证每年80万台发动机的生产任务,设备维修工段的成员们需要及时并且高效的解决维修技术难题。为此他们每年累计献工70多天,每年解决技术难题30多项,完成各种设备改造技术革新20多项。通过大家的锐意创新,攻坚克难,有5篇维修技术论文荣获公司级奖励,经过全员不懈努力,2018年度通过创新攻关,节约维修资金约1016.3万元,备件消耗费用资金2470万元。外委维修费用1130万元。为公司降本增效做出了突出贡献。
设备维修工段一直致力于建设时代新型科学管理工段,创建劳模创新工作室,旨在为劳模和员工搭建一个锐意创新,攻坚克难的阵地,引领广大员工,立足本岗职位,不断解决工作难题,放大劳模的品牌效应;成立动力先锋工作室,汇集一线岗位的技术能手,工作室成员自行制作了中国梦航天梦长征二号F运载火箭动态模型,自主研发制作了智能机械手,以及自主制作的“战神”小车在2018年沈阳市总工会举办的“超级技工”大赛中荣获冠军。
努力学习专业知识,开展传、帮、带、学,打造一个能打硬仗的维修突击队伍。设备维修工作,需要不断的学习新技术、新设备结构。在每位师傅熟练掌握新的技能后,总能把掌握的新技术传授给其他的同事,并且共同探讨和研究。工段内部定期组织技术培训,老师傅将自己多年的维修经验传给徒弟,采用理论与实践相结合的方式,让他们更快的成长,拥有独立诊断、独立处理的能力。在传授经验与技术的同时,还帮助新员工增强责任意识与安全环保意识,给予生活上的关心和照顾,让他们在维修工段找到归属感。事实上,维修工段就是一个充满爱的大家庭。维修工段,团结、友爱、技术够硬,也敢于迎难而上,从而确保了各生产线设备的正常运转。
自主研制螺栓垫圈分离机。公司生产的4G6机型发动机,在装配线发动机试验结束后,需要卸下油底壳放油塞,使发动机内部的机油全部流出,然后再重新安装放油塞。该放油塞拧下后,铝制的密封圈严重变形,再次使用不能达到良好的密封效果,严重影响发动机的质量。本着节能降耗的观点,响应公司的价值工程年,设备维修工段自主研制螺栓垫圈分离机,将放油塞与密封圈分离,更换新的密封垫圈,使放油塞多次利用。目前约有12万个螺栓已经过分离处理,为公司节省成本13.8万元,此项发明还被评为实用新型专利。
高精密加工中心主轴国产化技术改造。机加部数控加工中心的主轴在长时间加工中会有不同程度的磨损或异常撞机,磨损的主轴加工出的工件的质量难以保证,因此需要定期进行修理。如由国外设备厂商进行修理,每个主轴需要花费近15万元。为节省费用、缩短维修周期,工作室成员通过拆卸、分解、测量、分析,最终攻克种种技术难题,形成了一套自主维修的方案,在国内制作零件,无需邀请国外厂家进行修理,这项改造不仅使周期从国外维修的60天缩短至自主维修的1至2天,每年还能为公司节省成本800多万元。
ATC换刀机械手修复。加工中心机械手换刀箱在长时间使用后,会出现抓刀位置不准确,掉刀的现象,严重的造成刀具和主轴的损坏。换刀箱总成部件属设备厂家专用技术设计,总成部件购买订货周期长,价格贵。工段成员通过研究其机械构造,分析磨损情况,经过反复试验,形成一套自主的维修方案,对内部磨损零件,如蜗轮蜗杆,内咬合曲线凸轮的测绘、制作、安装,控制换刀轴反向间隙,以达到现场设备使用要求,缩短维修周期的同时还节省了费用。
自主研发3D打印机。为了响应公司节能降耗、降低成本的号召,倪军劳模创新工作室组建攻关小组,自主开发3D打印机。3D打印机技术运用金属、塑料、陶瓷等材料,在快速成型设备里分层制造任何复杂形状的物理实体。在维修过程中,对磨损或失效的零部件进行快速成型分析,分析其失效原因,并及时提出合理对策。设备各个零部件的复杂多样性,增加了故障维修的难度系数和零件制作的成本,3D打印技术的运用能极大缩短备件的制作周期、减少公司的运营成本。
曲轴孔精加工精度保证技术改造。在缸体的曲轴孔加工工序,以前在实施修理后,精度只能确保3个月,之后又会超差。该设备为国外专用机类型加工设备,是长刀杆镗削加工,长刀杆又属国外非标刀具,价格昂贵。曲轴孔是整个工件各回转轴之间的加工和测量基准,按照设计要求,曲轴孔的加工同轴度的为0.008mm。这种情况下,很难保证精度的稳定可靠性,工人反复调查,仍不明原因。维修人员通过对设备测量数据监控、检查,发现滑台相对导轨磨损,与刀具、刀杆、导套相对磨损间隙有偏差,只有缩小刀杆和导套加工的配合间隙,保证才能所要求的质量精度。另外,就磨损的刀杆来配作相应尺寸的导套,既延长刀杆的使用寿命,又保证加工精度。现改造实施1年多,加工废品下降90%,维修时间节省约24天。此项改造还荣获航天科工集团技术创新奖。
设计AGV自动牵引车。AGV自动牵引车,是指能够装备有电磁自动引导装置,能够沿路径行驶,具有安全保护以及各种移载功能的运输车,是目前物流自动化系统中关键设备。本项目应用单驱动可双向转弯行驶具有负载形式,可前进、后退、转弯,有效缩短行驶距离,可以在狭小空间任意单环线来回双向行驶,顶端设计有料架可适用于狭窄通道,实现产线物料转运自动化。
维修工段曾获得辽宁省工人先锋号,中国科工集团十佳班组,沈阳市先进集体、沈阳市“超级技工”大赛冠军、还被评为辽宁省劳模创新工作室;工段成员中获省级劳模1人,市级劳动模范1人,市级五一奖章1人,中国航天科工集团劳动模范1人,公司劳动模范2人,公司先进2人。
设备维修工段的成员,有着坚定的毅力和积极进取的精神,始终秉承“提供卓越产品,诚信奉献社会”的理念。不怕脏,不怕累,是他们每个人对自己的要求,从实际出发,从小事做起,是他们一直遵循的原则。他们勤奋学习、刻苦钻研、锐意创新的精神,始终激励着大家。劳动创造价值,奋斗成就伟业,他们在平凡的岗位上实现着自己的价值,同时树立起航天三菱人的精神旗帜,他们为企业的发展保驾护航!